If you want to prepare a gourmet meal, you start with fresh, quality, ingredients. You wouldn’t go to the sketchy low-budget grocery store around the corner or use whatever has been lying around in your refrigerator for weeks. You would go to your favorite market and choose the freshest ingredients you could get your hands on. The quality of the ingredients directly influences the quality of the final product.
Similarly, if you want to manufacture high quality precision gears, you should start with high quality gear blanks. You may be able to find or manufacture low cost, low quality gear blanks that seem to fit your requirements, but the quality of your finished gear will suffer, and your cost may be even greater in the long run. Let’s take a closer look at why…
High Quality Gears Start with High Quality Gear Blanks
After manufacturing engineering and design engineering have agreed on a gear design that is both manufacturable and meets the requirements of the system, the manufacturing engineer must create a process that ensures the gear ends up as designed.
To do this, each process step must ensure that mounting faces, or shoulders in the case of shaft gears, IDs, or bearing journals with shaft gears are perpendicular as best as practical to meet the needs of the final gear design. At gear cutting (hobbing, shaping) and/or any post heat-treat gear finishing operation (hard hobbing/skiving, gear grinding) the axis created on the blank needs to be maintained. In the case of heat treated gears it is quite often necessary to remachine (turn, grind) the mounting surfaces. Again, it is necessary to make sure the axis is not compromised.
Here is an example process for a gear with an ID and end faces as mounting and clamping surfaces:
- Sawed blank/forging/casting
- Turn end faces, ID and OD parallel and concentric and chamfer all corners for handling and manufacturing purposes.
- Hob gear teeth. Hold gear tooth alignment (lead), profile, and gear runout.
- Heat treat
- Grind end faces and ID parallel and perpendicular to each other.
- Grind gear teeth. Hold gear tooth alignment, profile, and gear runout.
The image below is an example of a gear we manufacture shown in three different process stages. The bottom is the forging at step 1, the middle is pre-heat treat at step 3, and the top is the final product.
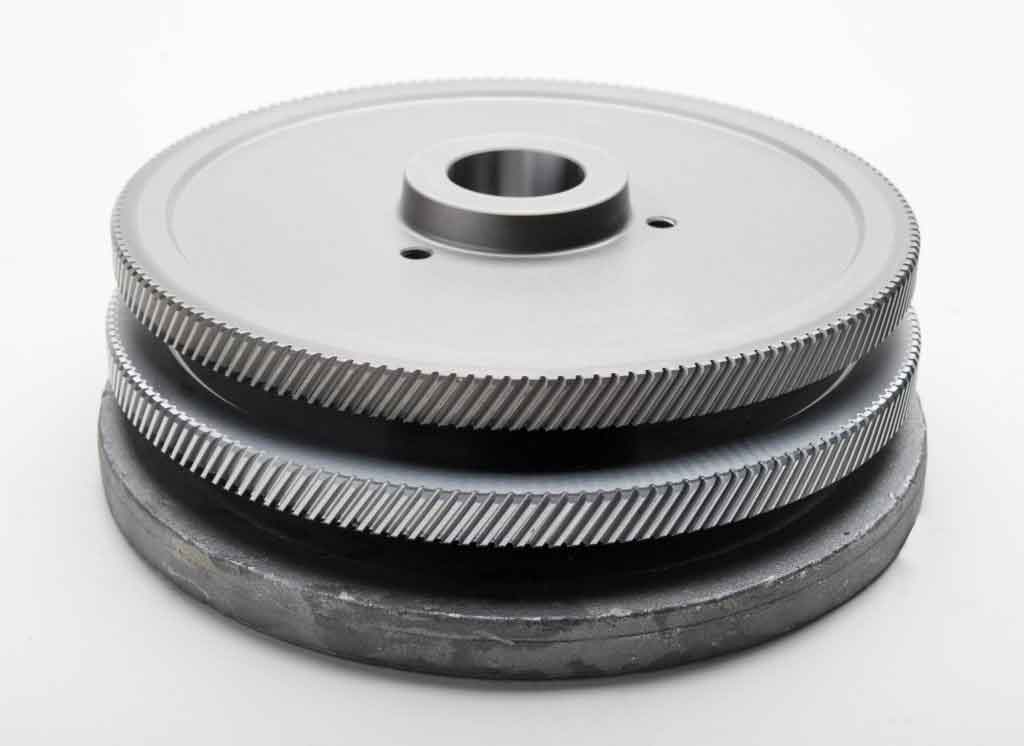
The accompanying drawing shows step 2 for this gear with dimensional tolerancing and geometric tolerancing to produce a good gear blank for the end product.
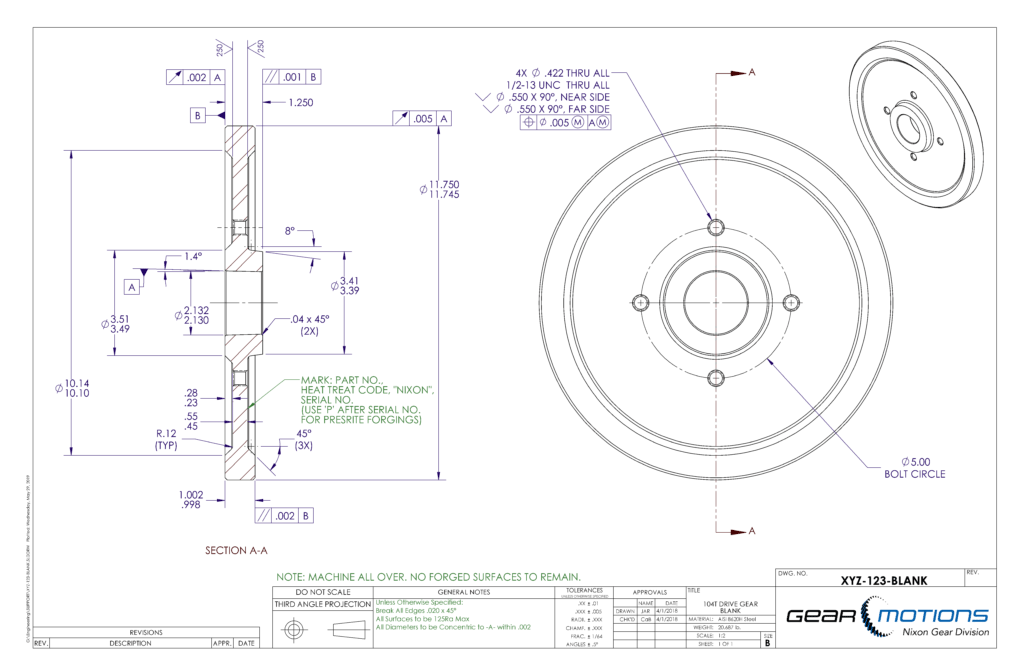
The quality of the gear at hobbing and at gear grinding will be best achieved if the blank prior to those operations is produced with parallel and perpendicular surfaces and that the axes have been maintained throughout.
Note that chamfering corners was mentioned above. This will help to ensure that burrs at those corners do not affect the maintenance of parallel, perpendicular and concentric surfaces. It also makes the gear safer to handle.
Quality Machining Processes
While starting with good quality gear blanks is the first step, it’s important to keep in mind that the quality of the finished gear is also influenced by every machining operation that is applied. For that reason, you’ll want to make sure that you work with an experienced gear manufacturing partner who will utilize quality processes and techniques every step of the way.
For quality gear manufacturing, look no further than right here at China Gear Motions. We have over 100 years of experience, and we are capable of manufacturing gears to the highest quality standards in the industry.
As an experienced gear manufacturer, we appreciate working with good quality gear blanks from the start. While it’s certainly possible to cut gear teeth on an imperfect gear blank, it is much more difficult and time consuming to make sure the end result meets the customer’s specified quality standards. On the other hand, working with quality gear blanks right from the beginning is easier and less time consuming. With improved efficiency and less waste, we are able to pass the cost savings along to our customers.
Contact our experienced sales engineers to discuss your gear manufacturing needs, and learn how China Gear Motions can help improve your product quality and bottom line.